** When you buy products through the links on our site, we may earn a commission that supports NRA's mission to protect, preserve and defend the Second Amendment. **
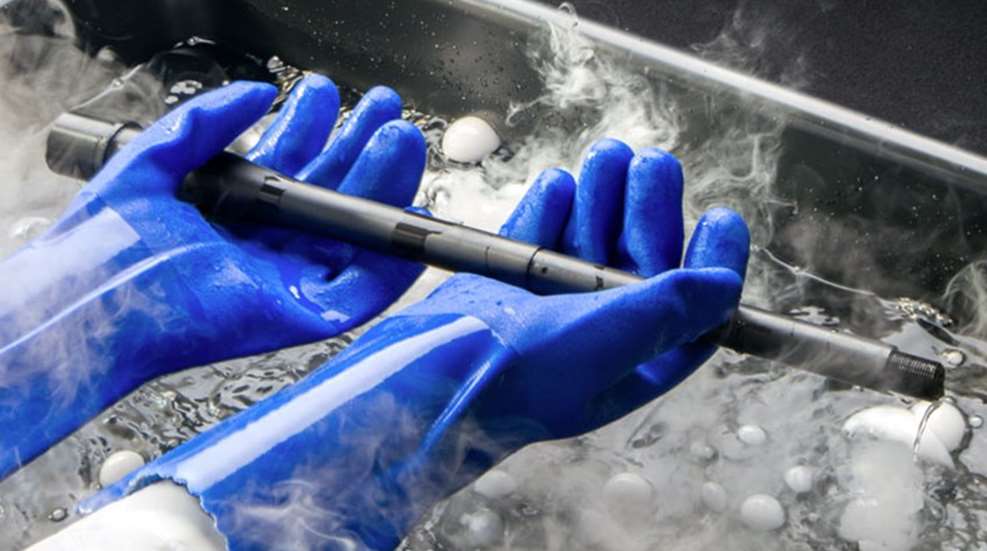
In a previous article, we discussed barrel-manufacturing methods from the early years of firearms technology. Today's article will cover the modern methods.
Most rifle and handgun barrels (save those intended for hammer forging, which we'll discuss in more detail in a later article) start life as a cylindrical steel bar about 1 inch thick and 12 or more feet long, obtained from a steel mill. Each barrelmaker or gun manufacturer specifies the exact grade and composition of steel to be used in order to obtain the desired combination of physical properties. Often the steel bars are stress-relieved before leaving the steel mill. Many shotgun barrels begin as thick-walled, seamless steel tubing.
Initial Trueing
At the barrelmaker's, the bar is cut into lengths of 28 to 30 inches, then turned on a lathe to face the ends off square and give the exterior a uniform roundness. If the steel was not stress-relieved at the mill, it may be given such treatment at this point by heating in a furnace to 600 degrees Fahrenheit and then cooling over a period of hours.
Deep-Hole Drilling
Next, the trued, stress-relieved bar is drilled using a long drill with a hollow stem and a tungsten-carbide bit, having a single cutting tooth on only one side. Under high pressure, cutting oil is forced through the hollow stem to cool the cutting tooth and to flush chips away. Some drilling machines spin the drill, some the barrel, and some spin both in opposite directions. Drilling a 28-inch or 30-inch-long hole that is uniform in diameter, smooth, and straight to within .0005 inches or so throughout its length is the most difficult part of the barrel-making operation. Most barrels that are to be button, broach or cut-rifled are drilled several thousandths under bore size.
Reaming
To bring the drilled hole to the proper diameter with a smooth interior surface finish, the drilled hole is now reamed. Care must be taken not to leave reamer marks on the bore surface in this step. Chatter marks from a dull or improperly used reamer are common defects.
Rifling
When the hole is straight and uniform, the next step is to put the rifling grooves in the bore using one of several methods. The most common methods of rifling a barrel include cut, broach or button rifling.
Air-Gauging
After rifling, the bore may be subjected to an air-gauge examination. An air gauge is a precision measuring instrument that uses a snug-fitting probe sensitive enough to detect extremely small inconsistencies in bore diameter as it travels through the barrel.
Straightening
At this point, the barrel may not be perfectly straight as a result of the stresses imposed by the various machining processes, or from a change in pre-existing internal stresses. Barrels can be straightened by an experienced craftsman using a turret press.
Lapping
To remove the small inconsistencies remaining in the bore, barrels are lapped as a final step. The lapping process involves pouring a small amount of molten lead into the bore to create a plug that fills the bore perfectly. The plug is coated with lapping abrasive and run back and forth in the bore using a metal rod. Depending upon the fineness of the abrasive, the lapping process will eliminate tight spots and take the interior finish to a mirror-like polish. Lapping is often performed after final contouring, as bore diameter may grow slightly when metal is removed from the outside of the barrel. Lapping is a time-consuming process usually only performed on match-grade barrels. The bores of factory production barrels are rarely, if ever, lapped.
Stress Relief
As a final step, virtually all aftermarket barrel manufacturers and many commercial gunmakers stress-relieve finished barrels to remove internal stresses that can cause warping and wandering points of impact as the barrel heats up. Most stress-relieving methods utilize conventional heat treating at elevating temperatures, as described earlier. Cryogenic stress relief is also popular, although some manufacturers feel it does little for certain types of steel.
The end result, the rifled cylindrical bar, is called a barrel blank. It will undergo additional operations such as chambering, head spacing, crowning, threading and/or further contouring and polishing before it begins service as a barrel.
Note that the above sequence is a description of the procedure used to produce a cylindrical barrel for a bolt-action rifle, and may not be a complete description for all barrels. Many barrels for handguns and semi-automatic rifles, for example, have complex profiles for locking lugs, sights, gas blocks and so forth that require more than just lathe work. The basic steps in barrel production are still followed, however.
Most rifle and handgun barrels (save those intended for hammer forging, which we'll discuss in more detail in a later article) start life as a cylindrical steel bar about 1 inch thick and 12 or more feet long, obtained from a steel mill. Each barrelmaker or gun manufacturer specifies the exact grade and composition of steel to be used in order to obtain the desired combination of physical properties. Often the steel bars are stress-relieved before leaving the steel mill. Many shotgun barrels begin as thick-walled, seamless steel tubing.
Initial Trueing
At the barrelmaker's, the bar is cut into lengths of 28 to 30 inches, then turned on a lathe to face the ends off square and give the exterior a uniform roundness. If the steel was not stress-relieved at the mill, it may be given such treatment at this point by heating in a furnace to 600 degrees Fahrenheit and then cooling over a period of hours.
Deep-Hole Drilling
Next, the trued, stress-relieved bar is drilled using a long drill with a hollow stem and a tungsten-carbide bit, having a single cutting tooth on only one side. Under high pressure, cutting oil is forced through the hollow stem to cool the cutting tooth and to flush chips away. Some drilling machines spin the drill, some the barrel, and some spin both in opposite directions. Drilling a 28-inch or 30-inch-long hole that is uniform in diameter, smooth, and straight to within .0005 inches or so throughout its length is the most difficult part of the barrel-making operation. Most barrels that are to be button, broach or cut-rifled are drilled several thousandths under bore size.
Reaming
To bring the drilled hole to the proper diameter with a smooth interior surface finish, the drilled hole is now reamed. Care must be taken not to leave reamer marks on the bore surface in this step. Chatter marks from a dull or improperly used reamer are common defects.
Rifling
When the hole is straight and uniform, the next step is to put the rifling grooves in the bore using one of several methods. The most common methods of rifling a barrel include cut, broach or button rifling.
Air-Gauging
After rifling, the bore may be subjected to an air-gauge examination. An air gauge is a precision measuring instrument that uses a snug-fitting probe sensitive enough to detect extremely small inconsistencies in bore diameter as it travels through the barrel.
Straightening
At this point, the barrel may not be perfectly straight as a result of the stresses imposed by the various machining processes, or from a change in pre-existing internal stresses. Barrels can be straightened by an experienced craftsman using a turret press.
Lapping
To remove the small inconsistencies remaining in the bore, barrels are lapped as a final step. The lapping process involves pouring a small amount of molten lead into the bore to create a plug that fills the bore perfectly. The plug is coated with lapping abrasive and run back and forth in the bore using a metal rod. Depending upon the fineness of the abrasive, the lapping process will eliminate tight spots and take the interior finish to a mirror-like polish. Lapping is often performed after final contouring, as bore diameter may grow slightly when metal is removed from the outside of the barrel. Lapping is a time-consuming process usually only performed on match-grade barrels. The bores of factory production barrels are rarely, if ever, lapped.
Stress Relief
As a final step, virtually all aftermarket barrel manufacturers and many commercial gunmakers stress-relieve finished barrels to remove internal stresses that can cause warping and wandering points of impact as the barrel heats up. Most stress-relieving methods utilize conventional heat treating at elevating temperatures, as described earlier. Cryogenic stress relief is also popular, although some manufacturers feel it does little for certain types of steel.
The end result, the rifled cylindrical bar, is called a barrel blank. It will undergo additional operations such as chambering, head spacing, crowning, threading and/or further contouring and polishing before it begins service as a barrel.
Note that the above sequence is a description of the procedure used to produce a cylindrical barrel for a bolt-action rifle, and may not be a complete description for all barrels. Many barrels for handguns and semi-automatic rifles, for example, have complex profiles for locking lugs, sights, gas blocks and so forth that require more than just lathe work. The basic steps in barrel production are still followed, however.